KUNDENERFOLGSGESCHICHTE
INTAI: Präzisionslaserschneiden von „komplexen“ medizinischen Instrumenten
Die Herausforderung
INTAI Technology Corp. (Taichung, Taiwan) stellt eine Vielzahl von Produkten für Branchen wie Medizintechnik, Automobilfertigung, Luft- und Raumfahrt, Präzisionsgeräte und Telekommunikation her. INTAI hat einen globalen Kundenstamm und beschäftigt heute mehr als 700 Mitarbeiter weltweit, dank eines nahezu kontinuierlich starken Wachstums seit der Gründung des Unternehmens im Jahr 1988. Medizinische Instrumente machen derzeit mehr als 65 % des Geschäfts aus. Hier bietet das Unternehmen Auftragsfertigung für Anwendungen wie endoskopische minimalinvasive Chirurgie und Brustbiopsie sowie Einweg- und wiederverwendbare Instrumente für eine Vielzahl von Verfahren. Donald Wang ist Vizepräsident bei INTAI für den Geschäftsbereich Medizinprodukte. Er erklärt: „2019 wollten wir unsere internen Fertigungskapazitäten um Präzisionslaserschneiden für röhrenförmige Geräte erweitern. Präzision war ein sehr wichtiger Aspekt, da wir einen guten Namen als Lieferant von qualitativ hochwertigen Komponenten haben, insbesondere für kleine Teile mit Rohrgrößen von nur 1 mm Durchmesser, aus Edelstahl und Nitinol sowie einigen anderen Metallen. Außerdem brauchten wir einen Partner für Lasertechnologie, der uns mit fachkundiger Unterstützung helfen konnte, die Prozessentwicklung zu beschleunigen. Und schließlich brauchten wir ein benutzerfreundliches Steuerungsprogramm, mit dem wir schnell zwischen verschiedenen Aufträgen wechseln können.“
Die Lösung
INTAI entschied sich schließlich für einen Coherent StarCut Tube. Um ein Maximum an Flexibilität, Vielseitigkeit und Rentabilität zu erreichen, entschied man sich für ein Hybridmodell, das sowohl mit einem Nanosekunden-Faserlaser als auch mit einem Femtosekunden-Ultrakurzpulslaser (USP) ausgestattet ist. Als Faustregel kann man sagen, dass der USP-Laser eine extrem hohe Präzision und hervorragende Kantenqualität liefert und für sehr dünne Rohre geeignet ist, so dass eine mechanische Nachbearbeitung, wie z. B. das Entgraten, oft überflüssig wird. Wang erklärt, dass dieser Laser die erste Wahl für die meisten Nitinolprodukte ist. Der Faserlaser hingegen bietet eine höhere Geschwindigkeit für allgemeine Schneidaufgaben. Es ist sogar möglich, beide Laser während desselben Auftrags einzusetzen, wobei der Faserlaser schnell größere Schnitte ausführt und der USP-Laser alle detaillierten Merkmale erstellt.
Wang erklärt: „Wir wollten eine vielseitige Maschine, die für Aufträge von Prototypen bis hin zu mehreren hunderttausend Stück pro Jahr wirtschaftlich sinnvoll ist. Die benutzerfreundliche grafische Benutzeroberfläche macht es sehr einfach, zwischen ganz unterschiedlichen Aufträgen und Losgrößen zu wechseln. Und der optionale StarFeed Röhrenzuführer ermöglicht einen unbeaufsichtigten Betrieb für größere Losgrößen, was unsere Arbeitskosten senkt.“
Das Ergebnis
Drei Jahre sind vergangen und INTAI ist sehr zufrieden mit der Wahl: „Die Ergebnisse und die Produktivität, die wir erzielt haben, haben unsere Erwartungen mehr als erfüllt. Wir können uns auf diese Maschine als Arbeitspferd in der Produktion verlassen. Wir nutzen sie praktisch jeden Tag für eine volle 8-Stunden-Schicht. Als Nächstes planen wir eine zweite Schicht, um die Leistung dieser Maschine noch mehr zu nutzen.“ Er schätzt die lokale Unterstützung in Taiwan, insbesondere bei der Prozessentwicklung. „Es ist wirklich hilfreich, einen Partner für Lasertechnologie mit einem lokalen Anwendungslabor zu haben, das sowohl mit Faser- als auch mit USP-Lasern ausgestattet ist. Auf diese Weise erhalten wir schnell ein Prozessrezept, das für entscheidende Parameter wie Kantenqualität, Durchsatz oder andere wichtige Parameter optimiert ist.“
Er fügt hinzu: „Am Anfang stand die Suche nach einer hochpräzisen Laserbearbeitung, und der StarCut Tube hat genau das und noch mehr geliefert. Wir sehen die Ergebnisse quantitativ, sowohl in Bezug auf die Ausbeute als auch auf die Qualitätsmetriken.“ Er erklärt, dass sie bei INTAI bei einer großen Anzahl von Kleinteilen ihre Prozessergebnisse anhand des bekannten Prozessfähigkeitsindex Cpk analysieren. Dies ist ein Maß sowohl für die dimensionale Konsistenz als auch für die absolute Genauigkeit, wobei Werte unter 1,0 bedeuten, dass ein Prozess „nicht fähig“ ist, >1,5 ist gut für einen neuen Prozess, und ein Wert von 2,0 bedeutet, dass ein Produktionsprozess die 6-Sigma-Qualität erfüllt. Ohne zu sehr ins Detail zu gehen, erklärt Wang, dass einige seiner StarCut Tube-Verfahren sehr beeindruckende Cpk-Werte erzeugen.
„Am Anfang stand die Suche nach einer hochpräzisen Laserbearbeitung, und der StarCut Tube Hybrid hat genau das und noch viel mehr geliefert.“
— Donald Wang, Vizepräsident, INTAI Technology Corp., Taichung, Taiwan.
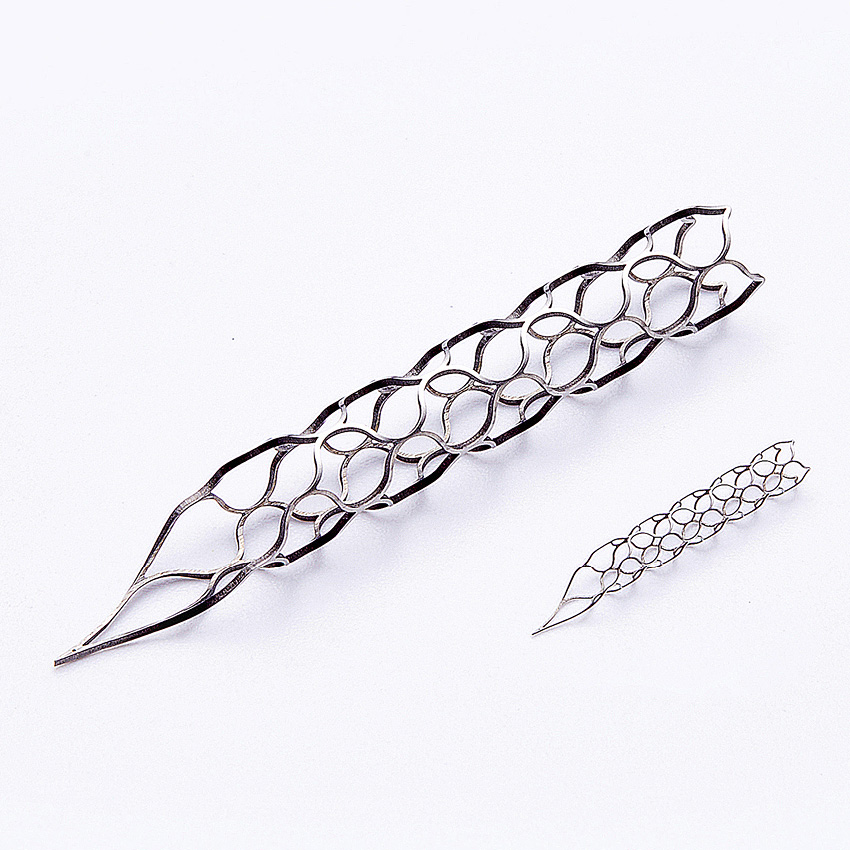
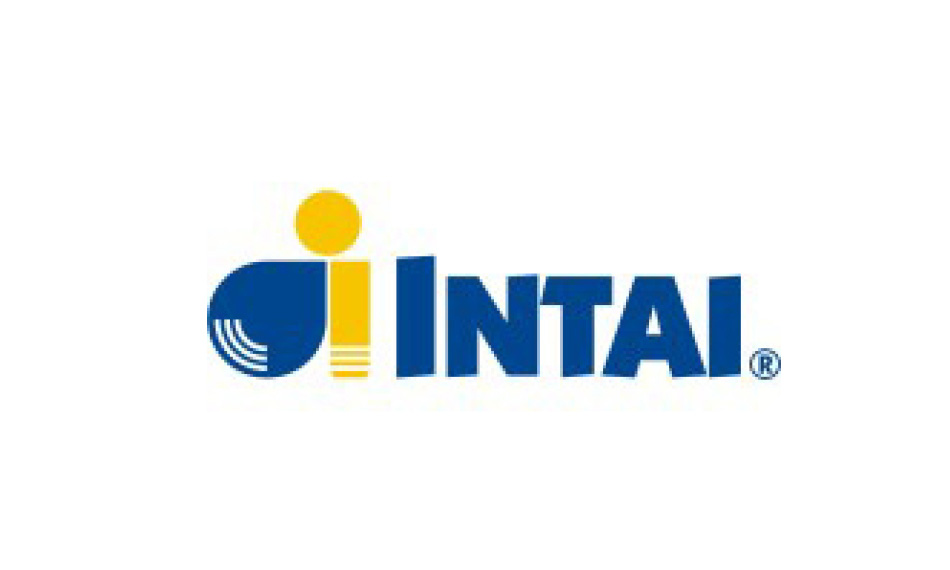
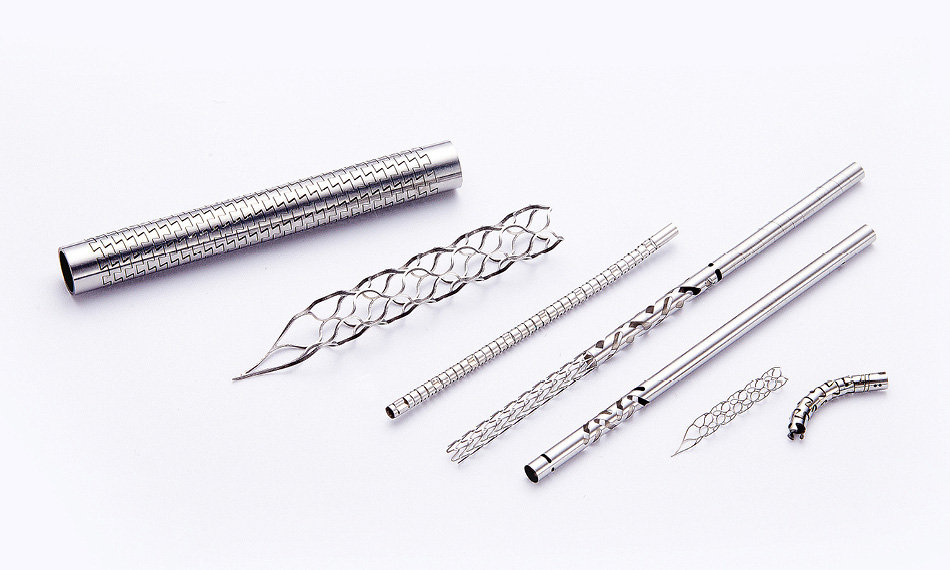
Abbildung 1. INTAI verwendet seinen StarCut Tube Hybrid zur Herstellung einer Vielzahl von schlauchbasierten Komponenten für medizinische Geräte und Einwegprodukte.