Better Welds for EVs
Coherent HIGHtactile simplifies and improves the wire welding process for increasingly demanding EV manufacturing tasks.
July 27, 2023 by Coherent
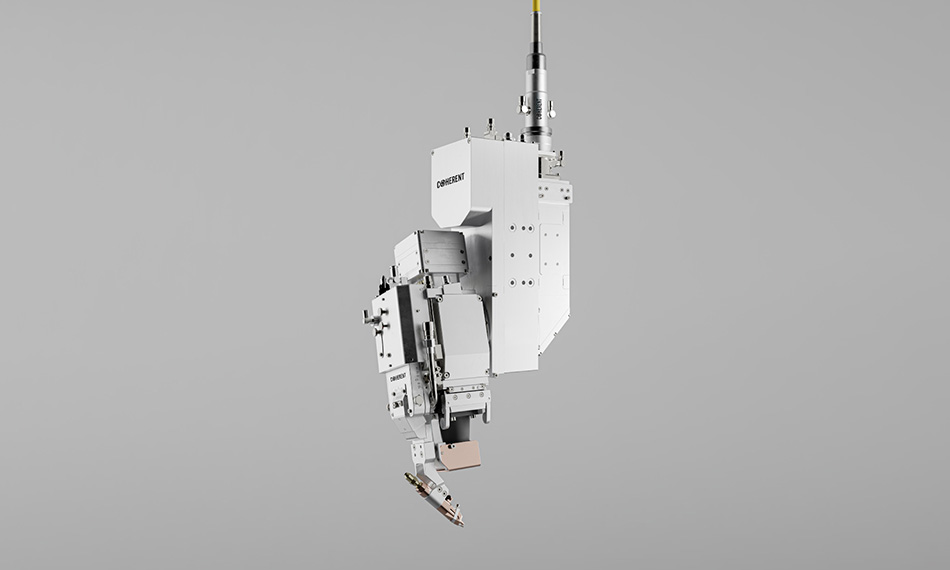
The new Coherent HIGHtactile is the latest evolution of our successful tactile laser welding heads; a tactile head mechanically senses the position of a weld joint as it moves over the part.
For welding with filler wire and brazing, HIGHtactile applies pressure to the wire along the joint between parts. By measuring the forces applied, it detects changes in joint position as it travels along the seam.
For welding that doesn’t involve filler wire, a mechanical “finger” rides in the weld seam and performs the same function. As a result, HIGHtactile consistently produces perfect wire or wireless welds on curved or complex-shaped parts – such as car roof joints, tailgates, and trunk lids.
Wire Welding
Wire welding is a highly adaptable process for auto manufacturers as they increasingly employ a variety of sophisticated metal alloys to improve the strength of vehicle components, while also reducing weight. Unfortunately, some of these alloys – especially those of aluminum and steel – can prove challenging to weld.
For example, melting can “boil off” some of the more volatile (lower melting point) elements that give the alloy its desirable properties. The resulting weld joint alloy doesn’t have the same characteristics as the rest of the material. This is especially a problem for automotive applications if it produces a weld joint that has lower mechanical strength than the rest of the part.
For some of the most useful aluminum alloys, hot cracking can often occur during welding. Hot cracking happens when large cracks, and also microcracks, form in the weld seam as the part cools. Needless to say, these challenges lower weld joint strength.
Wire welding also addresses the issue in automotive production of part fit-up tolerances. This means mechanical gaps between the joining parts produce unwanted breaks in the weld seam. This is especially true with extruded parts, which can have relatively large part-to-part dimensional variations, leading to poor fit-up.
In fact, extruded parts are now being widely employed to construct “battery boxes” for EVs.
Brazing
Brazing is a fairly similar process to wire welding and has been used for decades in the auto industry to create cosmetically appealing seams. It’s widely used on joints that are visible to the consumer, like around a trunk lid.
In the case of the trunk lid, wire is melted into the joint but the underlying base metal itself remains unmelted. The new wire material is deposited between the sheet metal resulting in a cosmetically pleasing joint. The ideal brazed joint is sufficiently smooth that no further preparation is required before painting.
HIGHtactile Makes Wire Welding Easy
Coherent HIGHtactile is a result of 20 years of Coherent’s experience designing seam-tracking systems for welding and brazing at Coherent. It offers enhanced productivity and superior results for EV manufacturing, body-in-white, and other assembly applications. Our heads are compatible with a variety of fiber-delivered lasers up to 8 kW — and new HIGHtactile is easier than ever to put into production.
In addition to its sophisticated suite of embedded sensors for maintaining position, HIGHtactile also incorporates a high-quality optical system that’s designed to faithfully maintain the original laser beam profile all the way to the work surface. For example, a laser with a flat-top beam profile can be used to optimize steel welding, whilst another profile can be employed to produce ideal results when brazing.
Learn more about HIGHtactile.